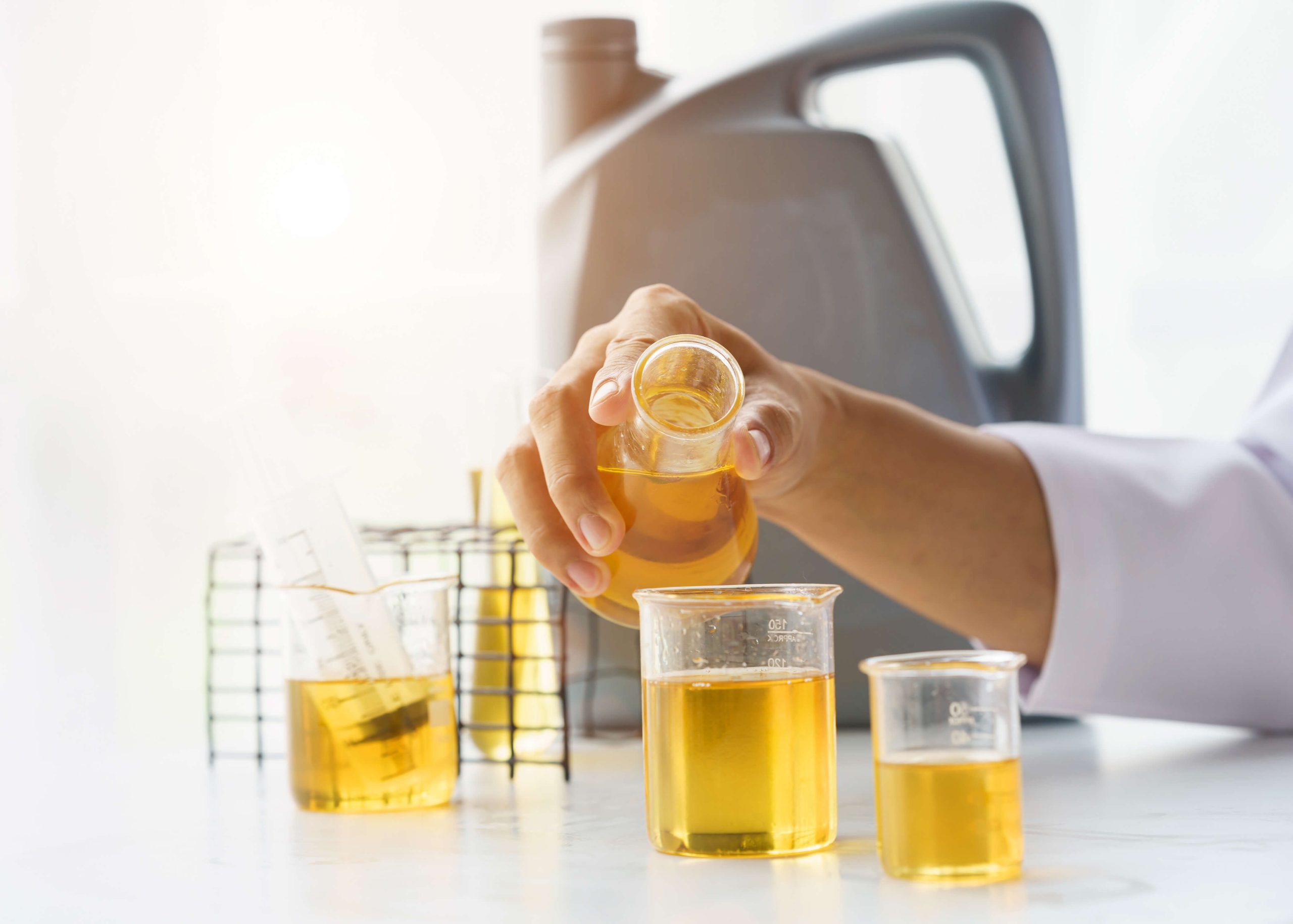
With our state-of-the-art laboratory and a team of experienced specialists, we offer comprehensive testing services to analyse and sustainably optimise the condition of your machines and systems.
OILTESCO GmbH, based in the region around Chiemsee (Bavaria, Germany), is your reliable partner for monitoring used oils. We offer comprehensive all-inclusive packages for machine monitoring using oil analyses – whether a standard package or customised. Our services include personalised sampling kits, individual analysis scopes and consulting.
Professional consulting
Have you received the results of your oil analysis and have further questions about the values determined or the condition of your oil? We can help you to gain a better understanding of the results of your oil analysis and take the necessary measures in good time.
Do you have any questions about an oil analysis or the oils you use?
We are pleased to support you.
Regular oil analyses provide you with fundamental insights into the condition of your systems and the oil used. These analyses enable you to determine the actual condition and identify potential wear problems at an early stage. This allows you to plan targeted maintenance measures and minimise downtimes. In addition, oil analyses help to improve the sustainability of your operating processes by enabling you to use the oil for longer and thus conserve resources in the long term. By avoiding unnecessary oil changes and replacing damaged components in good time, you increase the cost efficiency of your system operation and prevent major expenses.
With our customised diagnostics and individual recommendations, we will find the right solution for all your oil related needs. Whether it’s selecting the right oil or optimising oil change intervals – we provide you with transparent and expert consultation.
With convincing expertise and dedicated customer service, we continuously strive to fulfil your individual requirements and needs.
Our comprehensive service guarantees you fast and reliable support whenever you need it. From analysing your oil to maintaining your machines – we are there for you and ensure that your systems run smoothly and efficiently.
The highest quality is our promise. With the latest testing methods and strict controls, we ensure that our analyses and recommendations are always accurate and reliable. You can rely on our premium standards.
Accurate analyses not only reduce operating costs, but also protect the environment. We help you to extend the service life of your machines and optimise oil consumption.
Our team of highly qualified experts has many years of experience and in-depth expertise in oil analysis. We always keep up to date with the latest technologies through consistent further training.
Our sophisticated laboratory is equipped with the latest technology and analytical equipment to carry out precise and fast analyses and thus provide you with the most accurate results.
Minor drops, major effect
With the standard set, we focus on the condition of your engine. We evaluate the measured wear elements both qualitatively and quantitatively. This gives you an insight into normal and abnormal wear processes.
In addition to the values already recorded in the standard set, we record and interpret additional analysis parameters for the oil. This allows us to determine the condition of the oil more precisely and offer you possible change recommendations.
In addition to further analysis parameters, we also provide a more detailed interpretation of the data. This allows us to clarify questions such as whether the change intervals are appropriate or whether the correct oil is being used.
The ICP analysis (Inductive Coupled Plasma) provides information about metal abrasion (wear), additives and other contaminants. The change in additive elements, together with other tests, can provide information about the condition of the used oil.
Diesel fuel in the oil has a negative impact on the lubricating film. The viscosity is reduced. In addition, the positive lubricating properties of the oil additives are affected. The consequences are increased wear and even total failure of the tribological system. Causes for an increased fuel content are e.g. incorrectly adjusted carburetor, defective injection nozzle, or problems in the intake and exhaust tract (clogged air filter, blocked soot filter etc.). The diesel fuel content in the oil can be detected by means of gas chromatography. The figure is given in %.
Fourier transform infrared (FT-IR) spectroscopy can be used to draw conclusions about the oil condition. With known fresh oil, changes in the spectrum can be used to calculate mixtures, water and glycol input, additive degradation, soot content, oxidation and nitration values. If known, please always give us the full name of the fresh oil (manufacturer and exact product name)!
Qualitative determination of the glycol content based on FT-IR spectroscopy. Glycol in the oil is an indicator of leaks in the cooling system (e.g. defective oil cooler or cylinder head gasket). It leads to oil thickening (jelly formation) and can block filters and oil bores.
Particles can be generated in the system during operation (abrasive, adhesive or heavy wear) or can be imported from an external source.
Continuous particle entry is not exceptional with gear oils. With meshing gears, synchroniser rings in manual transmissions or clutches in automatic transmissions, microparticles are constantly being produced, which are usually filtered out by the installed transmission oil filter. Although good transmission oils can slow down this wear process, they cannot prevent it overall. Too many particles in the oil or a sudden increase in the particle concentration indicate irregular operation. This may be due to wear or the ingress of dirt from outside, e.g. due to a defective shaft seal.
Particle counting makes it possible to monitor these processes. For easier assessment, the particles in the oil sample are counted and categorised according to size. The measured concentration is then specified according to DIN ISO 4406 in three size classes (larger than 4 µm, larger than 6 µm and larger than 14 µm).
The Particle Quantifier Index is a dimensionless indication of the amount of ferromagnetic (magnetisable) abrasion in the oil. In contrast to the ICP method, particles larger than 5 µm can also be recognised here. The PQ index therefore also makes it possible to identify wear patterns that are due to short-term effects, for example.
The TAN is a measure of the acidic components contained in the oil. In engine oils, the TAN increases over the service life of the oil, mainly due to combustion by-products entering the oil. This is slowed down by the alkaline reserve (TBN) contained in the oil. The further the TBN decreases, the faster the process runs.
In hydraulic and gear oils, a TAN can already be measured in the fresh oil. This is caused by some additives. These are broken down when the oil is used, causing the TAN to fall. If the TAN rises again, this indicates oil ageing products. A change in the TAN is therefore a valid indicator for an upcoming oil replacement.
The TBN is an indicator of the alkaline reserve of the oil. In engine oils, it indicates whether the oil is still able to neutralise acidic combustion products that are introduced into the oil via blow-by gases.
Viscosity is one of the most important parameters for defining the lubricating properties of an oil. Changes during operation therefore have a significant influence on the safe operation of the system. Viscosity at 40° C plays a decisive role in the industrial environment in particular, as industrial oils are standardized according to this characteristic value (e.g. ISO VG 32; the viscosity of this oil must correspond to 32 mm/s² (+/- 10 %) at 40° C). However, the viscosity value at 40 °C is also determined for the automotive sector, as the VI can be calculated from this (see VI). If the viscosity changes at 40° C, this can mean mixing with other oils, oil thickening, etc.
The viscosity at 100° C is used to standardize viscosity classes for automotive lubricants (e.g. SAE 40; at 100° C the oil must have a viscosity of 12.5-16.3 mm/s² to comply with the standard). This value is important for industrial oils because the VI can be calculated from the two viscosities (at 40° C and at 100° C).
The viscosity of oils depends on the temperature. Rising temperatures cause a decrease in viscosity, the oil becomes thinner. However, this temperature dependency is not the same for all oils. With high-quality products, this influence is less noticeable, i.e. the viscosity of the oil decreases less with increasing temperatures than with cheaper products. The viscosity index (VI) was introduced to create comparability here. This value is calculated from the viscosity of the oil at 40° C and 100° C. A high VI is to be equated with a low temperature dependency. The VI should not change during operation, as regular oil ageing (oxidation) has the same effect on viscosity across all temperature ranges. However, shearing of special additives to improve the viscosity index (VI improver) can occur. As a result, the VI decreases, whereas an increase indicates mixing during refilling.
The first impression counts. We therefore record its visual appearance as early as the sample registration stage. Abnormalities such as particles, deposits, streaks or phase separation are documented. The sample is then also photographed.
Water is the mortal enemy of every tribological system. The lubricating effect is reduced, there is a risk of cavitation due to the formation of vapor bubbles, oil ageing is accelerated, it has a corrosive effect, etc. The water content in the oil should therefore always be monitored during an oil analysis. A sufficiently accurate and cost-effective method is determination by means of FT-IR spectroscopy. The water content is given in %. If it is necessary to determine the water content more precisely, the measurement is carried out using a titration procedure according to the Karl Fischer method. The water content is indicated on the laboratory report in ppm (parts per million).
While foam forms on the oil and can be measured there, the air separation capacity provides an indication of how quickly air bubbles can be removed from the oil. For this purpose, the density of the oil is measured in relation to the time after air is introduced.
Foam (air bubbles) reduces the lubricating properties of oils, the temperature release behavior deteriorates and oxidation is promoted. Foam is usually caused by mechanical action (meshing tooth flanks) or sudden pressure loss. Aging phenomena favor the formation of foam. However, mixing different oils can also lead to increased foaming. To monitor the foaming behavior, air is introduced into the oil via a porous stone. The height of the foam carpet and its decay (after 10 minutes) are then measured. The measurement can also be carried out at different temperatures (sequence I, II and III) and thus realistically reflects the conditions inside the machine.
MPC stands for membrane patch coloumetry. This method is used to determine the tendency of oils to deposit. In particular, the polar oil ageing products that form during long oil usage cycles can no longer be kept in suspension by the oil after a certain point in time. This results in deposits that restrict the functionality of the system. Vacuum filtration of the used oil via a very fine filter and the subsequent optical measurement of the filter provides an indication of this. Suitable measures, from fine filtration of the entire oil volume to the final oil change, can be derived from this.
RULER is the abbreviation for Remaining Useful Life evaluation routine. Antioxidants can be detected transparently using this procedure. Antioxidants are intended to slow down the regular oil ageing process by neutralizing the free radicals produced in the process. The usual test methods are aimed at monitoring the consequences of oxidation. Using the RULer, the degradation of antioxidants can be monitored directly, allowing countermeasures to be taken at an early stage!
Due to its non-polarity, oil does not combine with the polar water, but instead a phase separation occurs. However, oil ageing products (and also some additives) can influence this, as they are mostly polar in nature and therefore improve the solubility of water in oil. When determining the water separation capacity, the time until phase separation is therefore measured.
methods marked with *) are carried out in one of our partner laboratories
© 2025 OILTESCO GmbH